nieuws detail
Flexible workmethods Orangeworks enable fast delivery
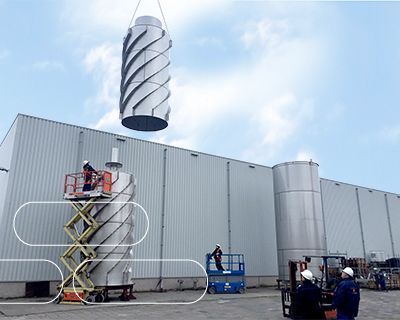
Building two heater weldments of more than 8 meters in height within 6 weeks is a challenge Orangeworks wanted to tackle eagerly. Frank Appeldoorn proudly tells about the start of the extensive project that Orangeworks has managed to bring to a good end thanks to flexibility and enthusiasm.
Identify challenges
"For a new customer in the dairy processing industry, we have done everything we can to achieve the requested delivery time," says Frank Appeldoorn, Sales representative at Orangeworks. In addition to the delivery time, the size of the tank and the available space in the assembly-hall were also a challenge. Frank: “Our customer converts milk into milk powder. For their new factory, they needed a tank that converts cold air into warm air, which then swirls and passes through channels to another part of the system. "
Act quickly
To guarantee the delivery time it was essential that different suppliers deliver all materials to Orangeworks within a very short period of time. Emiel van den Heuvel, project engineer: “We have thoroughly checked the customer's list of components and then immediately ordered everything. We had no time to lose and it had to be correct in one go. ”After one-and-a-half week, the construction of the separate tanks could already start. Emiel: "After all, we knew that we had to deliver the tank on February 1st."
Building a tank if this size was a first for Orangeworks. The tanks are over 8 meters high with a diameter of 3.5 meters. Jos van der Wijst, assistant-foreman: “We had to roll plates of 11 meters into cylinders and then weld them with our automatic plasma welder. This plasma welder ensures that we can weld very precisely. This meant saving time and a very high quality welding technique. "
Creative solution
Because the final tank would be more than 8 meters high, it could not just be assembled in the hall. After all, safety is paramount at Orangeworks. That is the reason why the project team, in consultation with Emiel, has chosen to make the tanks in parts in the hall and to assemble them outside. Emiel: “The first idea was to hoist all parts through the skylight in the hall. During the project we decided to change the lifting plan and thus assemble it outdoors. This meant that we had to bring all the parts outside and then fit them together like a Matryoshka doll. ”
Proud of the team and the end result
The project team is proud of what they have achieved. A voluminous product, for the first time and in a short period of 6 weeks. Jos: “The best moment of the entire project for me was standing outside with the crane and seeing everything fitting together exactly. I wouldn’t mind participating in such projects more often."